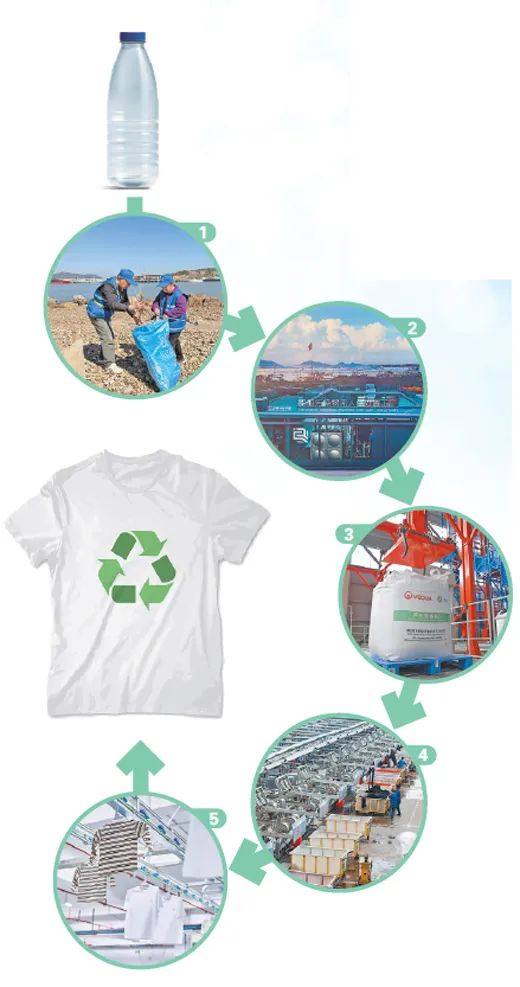
Picture (1): The staff of the "Little Blue House" in Jiaojiang District, Taizhou City are picking up garbage. Courtesy of Zhejiang Lanjing Technology Co., Ltd
Figure (2): "Marine Cloud Warehouse" unmanned chemical disposal plant for ship pollutants. Photo courtesy of the Propaganda Department of the Jiaojiang District Party Committee
Figure (3): In the factory area of Veolia Huafei Polymer Technology (Zhejiang) Co., Ltd., marine plastics are processed and turned into plastic chips. Photo by Cui Jili (People's Vision)
Figure (4): The production process of woven fabrics in the factory of Hangzhou Xinsheng Printing and Dyeing Co., Ltd. Photo by Fu Xiaoling (People's Vision)
Figure (5): In a factory in Jiangbei District, Ningbo City, the garment transportation link on the intelligent garment production line. Photo by Chen Ke (People's Vision)The Third Plenary Session of the 20th Central Committee of the Communist Party of China proposed to develop green and low-carbon industries, improve the incentive mechanism for green consumption, and promote the construction of a green, low-carbon and circular economic system.What are the green "doorways" in the production process of a short-sleeved piece? From recycling and utilization to textiles and garments, the "blue cycle" exploration from Zhejiang has made environmentally friendly clothing favored by consumers, and the whole process of "from the sea to the shelf" has also been established, making green consumption accessible and green lifestyle gradually becoming fashionable.Not long ago, when Xiao Yu, a citizen of Hangzhou, Zhejiang Province, was shopping online, a short-sleeved shirt with the slogan "The fabric comes from the ocean waste plastics" aroused his curiosity.After inquiring about customer service, he learned that the polyester fibers needed to produce this short-sleeved fabric come from waste plastics recycled from the coastline in Zhejiang, and then blend with cotton to make recycled yarn, which is not only environmentally friendly, but also energy-saving and emission-emission. "A short sleeve can also contribute to the environment, which is quite meaningful." Xiao Yu placed an order.On October 30 last year, the "Blue Cycle" marine plastic waste management model from Zhejiang won the 2023 United Nations "Champions of the Earth Award". This exploration is not only committed to solving the problems of difficult collection, high disposal cost and low recycling rate of marine plastic waste, but also establishes the whole process of "from the ocean to the shelf" - this short sleeve purchased by Xiao Yu is derived from this.Recycling – Increasing public motivation and participation in ocean plastic waste collectionEarly in the morning, on Waisha Road, Jiaojiang District, Taizhou City, many people gathered at the "Little Blue Home" Waisha site, and the garbage bags carried by everyone were particularly conspicuous. "I picked them up at the beach." Pointing to a large bag of plastic waste next to him, 71-year-old Chen Xiafang said.Site staff member Ruan Ningning took off the recorder on the vest worn by Chen Xiafang and confirmed the trajectory of the movement through the screen, "We used the visual recorder to ensure that the garbage was collected within one kilometer of the coastline in Jiaojiang District. Ruan Ningning introduced that the recorder can delineate the collection range in the region, realize trajectory monitoring, and ensure that the garbage comes from the sea from both regional control and technical control.After weighing, the site recycled the bag of marine debris at a price of 2 yuan per catty. "Our purchase price is much higher than the market price." Ruan Ningning said. At the site, after a simple cleaning and sorting, the sorted plastic bottles are compressed, bundled, and packed into smaller plastic piles for the next purchase.At the Waisha site, for example, there are about 50 registered marine litter collectors like Chen Xiafang. Ruan Ningning introduced that as long as the marine garbage is picked up for 6 months in a row, Zhejiang Lanjing Technology Co., Ltd., to which the site belongs, will also purchase insurance for it, because the purchase price is relatively high, it can be settled in time, and the public enthusiasm is very high.In the "Ocean Cloud Warehouse" located near the Jiaojiang Bridge, in a clean and clean environment, the machine is running in a low voice. Chen Hui, director of operation and maintenance of Blueview Technology, introduced that marine plastic garbage such as plastic bottles, waste fishing nets, and buoys are initially crushed and compressed in the "Ocean Cloud Warehouse", and then transported to the recycling plant for cleaning, crushing, granulation, etc., to produce plastic raw material particles according to customer needs."After front-end treatment, the capacity of plastic waste such as mineral water bottles has been reduced by 90%, and the transportation efficiency has increased by 70%." Chen Hui said that the raw materials will be shipped to the "Blue Alliance" member companies for further processing. "Blue Alliance" is a non-profit organization led by Blueview Technology, which aims to realize the whole process of ocean plastics from recycling to reuse.Leverage – automated production processes to achieve precise processing of ocean plasticsAt 9 a.m., a truck full of marine recycling plastic bottles slowly drove into the production plant of Veolia Huafei Polymer Technology (Zhejiang) Co., Ltd. in Anji County, Huzhou City. Workers drive forklifts and skillfully transport pieces of "plastic bottle bricks" to the bottle brick warehouse and place them neatly in the ocean plastic area.Veolia Huafei is one of the initiators of the "Blue Cycle" project. Fu Xianwei, Operations Director of Veolia Huafei, said: "In the 'Blue Cycle' project, we are responsible for the key aspects of cleaning and melting and recycling plastics. ”"This batch of ocean plastic bottles, totaling 8.6 tons, is the ocean plastic bottles that were recently recycled through the 'Blue Cycle' project." Fu Xianwei said that in order to ensure the authenticity and reliability of the source of plastic bottle recycling, it is equipped with an exclusive QR code to trace the whole process of plastic bottle collection.How does ocean plastic be disposed of differently compared to plastic bottles recycled from conventional sources?"After being soaked in seawater for a long time, there are more impurities such as sediment and oil stains on the bottle body, and the color value is yellow and the sea salt content is higher after recovery, which leads to a decrease in its physical properties and a lot more difficult to treat." Fu Xianwei introduced. In the cleaning workshop, the reporter saw that the unpacked marine plastic bottles were initially screened out of sediment, and then entered the pre-cleaning drum for cleaning.Subsequently, the plastic bottle passes through two steps of automatic optical sorting equipment and manual sorting to remove the bottles that do not meet the requirements of color and material, and after about 30 minutes, the ocean plastic bottle becomes a piece of clean cold water bottle flakes. After the cold water bottle flakes are bagged, they should also enter the hot washing line for deep cleaning to thoroughly clean off the impurities such as sea salt, sediment, ink, and labels on the surface of the bottle flakes."After the automatic optical separation of the flakes again, we get high-precision and usable plastic flakes." Fu Xianwei said that through a series of testing processes, these bottle flakes finally enter the molten granulation process and become crystal clear, glassy recycled plastic particles.So far, Veolia Huafei has processed about 10 million ocean plastic bottles recycled through the "Blue Cycle" project.Textile - set up a special production line to ensure the quality and performance of fabricsAt the end of last year, Hangzhou Xinsheng Printing and Dyeing Co., Ltd., which is also a member of the "Blue Alliance", received plastic pellet raw materials from Veolia Huafei. After the inventory was correct, the plastic pellets were transported to the surrounding factories for pretreatment. According to Fu Xiaoling, the company's marketing director, plastic particles should be mixed with cotton, hemp, wool and other fibers to be made into staple fibers, or directly drawn into filaments by machines, and finally formed into a circle of yarn before they can be used for textiles.In the textile workshop, circular knitting machines and rapier looms are arranged one after another, and the yarns are woven into rolls of grey cloth by different techniques such as knitting and weaving. One of the circular knitting machines is marked with the eye-catching "Ocean Plastic Knitting Line" logo, "It is on this machine that yarns made from ocean plastic are made into grey fabrics." Fu Xiaoling said.In the printing and dyeing workshop, it is also dyed in the air flow tank through a special printing and dyeing machine marked "Marine Plastic Dyeing and Finishing Production Line"; After processing, the fabric is put into the "Ocean Plastic Quality Inspection Zone", where it undergoes a series of inspections and tests to ensure that the quality meets the standards – and finally, the fabric with the product number "XS-W50001-C" is successfully made.Why do we need to separate the production line for ocean plastics? Fu Xiaoling explained: "Since the source of marine plastics is not standardized, there will be many technical difficulties in the processing process, so that it is convenient to process feedback in a timely manner, and second, to facilitate visual management. ”Fu Xiaoling said that in recent years, the company has invested tens of millions of yuan to set up a pilot plant for the research and development and testing of recycled fabrics, "However, compared with recycled materials from land, marine plastics are still slightly different." For example, yarns made from ocean plastic have a high oil content, so we need to screen different degreasers. Due to the low thermal stability of the material, it is easy to cause uneven color and poor color fastness during the dyeing process, so strict temperature control is required. ”After many tests, Fu Xiaoling can now "make a ticket": "We can proudly say that fabrics made of marine plastics are not inferior to traditional materials in terms of quality and performance, and are very popular in the international market." ”Garment - develop different types of environmentally friendly clothing, and expand the market online and offlineHalf a month later, this batch of cloth with the product number "XS-W50001-C" arrived at the production base of a company in Jiangbei District, Ningbo. There was no rush to production, and the cloth was first transported to the raw material testing area to await testing."We will conduct visual inspection of the fabric, and at the same time appoint a third-party professional testing agency to conduct physical and chemical inspection of the shrinkage, formaldehyde, pH value and other parameters of the fabric to ensure quality." Hou Biao, director of the company's supply chain, said that after 5-7 days, the fabrics that passed the test will be accepted and entered the garment process, and the unqualified ones will be returned."This batch of eco-friendly fabrics contains at least 5% ocean plastic, and we will process it in multiple processes." According to Hou Biao, taking a short-sleeved "170/92A" size and weighing about 200 grams per square meter as an example, although it looks no different from ordinary short-sleeved, it needs to use about 1.44 marine plastic bottles.After pre-shrinking, loosening, cutting and other links, about 1,600 pieces of cloth covering the body, cuffs and other parts required for this short sleeve are sewn as the most important and final process before entering the garment. Under the skillful operation of the sewing workers, a short sleeve made of marine plastic as a special raw material was quickly formed."Since May, this short sleeve has been launched to the market as a new model this summer, and it will be sold online and offline. Although it is a new product, the market feedback is good, and it has become a star product in many offline stores. Daniel Zhang, the founder of the company, said that although the cost of producing such an environmentally friendly short sleeve will increase by at least 10%, Daniel Zhang has his own considerations - "I grew up by the sea, and I was sad and anxious to see the coastline being eroded by plastic waste. Daniel Zhang said, "For us, the main thing is to pay more attention to whether the other party's garbage is really from the ocean." The visual traceability of upstream links dispelled Daniel Zhang's doubts.Now, the company has launched a "battery life plan", "If you don't wear unwanted old clothes and take them to offline stores, you can deduct 20 yuan in exchange for a short-sleeved piece made of recycled ocean plastic." Daniel Zhang said that on the one hand, it also provides a new path for the recycling of used clothes; On the other hand, you can also use the discount to open up sales for eco-friendly short sleeves."Next, we will develop more different types of eco-friendly clothing." In Daniel Zhang's view, only when more enterprises participate and continue to try to protect the ecological environment can we jointly protect our blue planet.
Source: Official Account (China Circular Economy)